Cut‑to‑length lines are generally thought of as systems that produce sheets or plate. Temper Mill cut-to-length lines and Stretcher Leveler cut-to-length lines have both been successfully utilized in applications where superior flatness and stability are required.
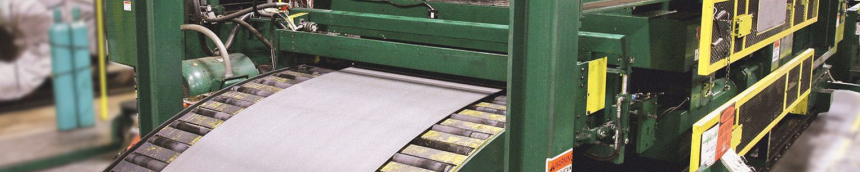
These applications typically include lasers, plasmas, or punch presses. When operated properly, both processes provide sheet/plate with minimal residual stress; however, the mechanisms to achieve this low residual stress state are different.
Metal forming using a temper mill is an important stage in the stainless steel manufacturing process. The science behind the temper mill involves compression, or rolling, the stainless through what is known as a cold reducing process, temper pass. This increases the density of the steel by reducing its overall thickness by around 1.5% to 2%, consequently, not allowing the steel to expand under pressure.
The stainless steel coils that are run through the temper mill go through a fairly simple procedure. The material thickness is compressed and elongated in the rolling direction. However, as temper mills do not have selective roll-bending across the strip width, a roller leveler must be used subsequent to the temper mill to create the final sheet/plate flatness and to correct for any remaining shape defects (edge wave, center buckle, coil set). The steel mill controls the extensions, or ends, of the steel as it is processed to prevent yield point elongation. Yield point elongation is a deformity that can occur where discontinuous regions succumb to strain from pressure and stretch or flatten out. After the steel has passed through the mill, its surface layer becomes more uniform. It is important to note that a temper mill cut line does not evenly exceed the yield strength of the material through the full thickness of the material (a gradient of multiple yield strains to zero exists from the surface to the centerline) and that the roller leveling that occurs after “tempering” actually introduces some residual stresses into the strip to create final sheet/plate flatness. Maximum shape correction is limited only by the % reduction capability (typically in the 2%-3% or 2000-3000 i-unit range); however, in practical application the specific order minimum gauge may limit the amount of correction allowed. In applications where superior flatness and stability are required, the temper mill cut line has provided superior product to “roller leveler only” product.
Leveling, or cut-to-length, is a type of metal shearing process where unlike slitting, the primary function is to take large rolls, or coils of material (stainless steel, aluminum, copper) and unwind, or uncoil into lengths end users require. The resulting material is shipped as flat-stock (sheet/plate) or further sheared into flat bar.
The science behind stainless steel leveling is to flatten the coil, making it ripple-free, then to neutralize the hidden internal stresses that cause twist and bow in parts during secondary operations such as stamping. Leveling is achieved by precisely bending coils of material back and forth as it’s passed through a series of small-diameter offset rolls.
Every stainless steel coil has unique physical characteristics. The yield point refers to the coils’ elastic state, which is a measurement of internal tensions. When flexed within this elastic zone, the coil will spring back to its previous state. Stainless steel forced beyond that point enters a plastic zone, or plasticization, where it becomes less resistant and more workable. The tensile strength marks the point where the material can fracture or crack.