Slitting has long been thought of as an art, but has increasingly become recognized as a science.
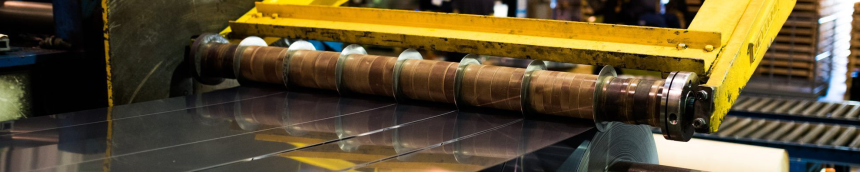
Slitting is a type of metal shearing process, whereby, rather than making cuts at the end of a workpiece like shearing, the primary function is to take large rolls, or coils of material (stainless steel, aluminum, copper, etc.) and slit them into widths and lengths end users require. To fully understand the slitting/shearing process is to understand fracture mechanics. Slitting is not simply a function of shearing the material in two. Shearing is only part of the story. As the coil runs through the slitter, two rotary blades – one upper, one lower – make the cut. In order to actually cut the material, sufficient compressive forces must be applied to cause it to fracture. When the compressive forces exceed the material’s ultimate tensile strength, a fracture takes place. Stainless Steel typically fractures at different degrees, depending on the type/grade of material being slit, and whether the knives align along the fracture plane. When performed correctly, the slit edge will have a shiny shear zone, a darker fracture zone, and a defined straight line separating the two.
Many factors must be taken into consideration in order to produce high-quality stainless steel slit coil. Horizontal knife clearance, depth of penetration, size of the stripper rings, material characteristics, as well as the slitting head or shear itself, will all enter into the equation. We strive to properly manage all of these variables on a day-to-day basis.
Burr, one of the most significant and recognized variable of the slitting process, occurs in large part due to compressive displacement of the material. The greater the compressive forces required to fracture the stainless, the greater chances we have of encountering Burr. This is due to the fact that the forces applied to the metal (to cause it to fracture) must be kept to a minimum. The primary cause of Burr is recognized by the horizontal knife clearance. When horizontal clearances are set too wide, this misaligns the knife edge with the fracture plane and creates a Burr on the bottom edge. When horizontal clearances are set too tight, a double fracture can occur. The knives over-penetrate to make the steel fracture and as a result, dull faster, and heavy Burr becomes induced. Consequently, harder or tempered stainless requires more horizontal clearance. The correct horizontal clearance for stainless steel and many of the higher strength low alloy steels is frequently set to 20 percent or more of the material thickness.
The tooling itself is also a major consideration. Shimless Tooling produces the most accurate slitter set-ups possible and guarantees a virtually Burr free, zero camber slit coil. We pride ourselves on our shimless tooling for high precision slitting, where tooling meets the tightest tolerances.
Advances in equipment, tooling and software have assisted our operators to better control the variables. Depending on whether or not you’re using light or heavy gauge material, our operators will set the rotary blades to achieve proper results and ensure production of high-quality stainless steel slit coil when it arrives at your facility.